Soluble coolants improves machining performance
The cutting or grinding fluid in a machine tool may require changing for a variety of reasons. When this is done, it is usually desirable to clean the system before refilling it with fresh fluid, particularly when changing from one product to another. The soluble coolant manufacturer recommended sump cleaning procedure is to be executed for targeting the longer sump change frequencies for machines that have been operated with mixtures of water and soluble oils. The system should be refilled as soon as possible after cleaning to prevent rust formation.
A soluble cutting oil is formulated to emulsify readily with water in a wide range of oil-water ratios. The emulsion formed is usually quite stable, yet it is sensitive to conditions that may make it break or even invest. The effectiveness of the cutting or grinding operation depends upon the use of a proper emulsion and a reasonable amount of care is required to maintain the emulsion in good condition. In general, there are three major factors that can effect emulsions:
1. Cleanliness, i.e., freedom from solid contamination and bacteria,
2. Water, both the quality and relative concentration, and
3. PH value.
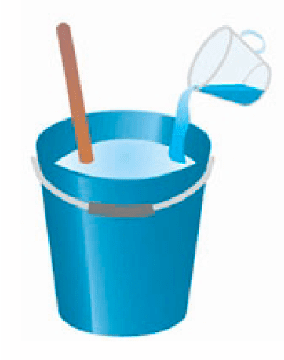
Soluble coolant is mixed with water before filling / topping up on machine tool. Remember to add oil gradually to water. Hand-mixing with stirrer is sufficient. Do not add water directly to oil.
Maintain cleanliness of sump
Emulsion characteristics can change significantly with only minor quantities of extraneous material. It is imperative to practice good housekeeping that will keep the fluid and the fluid system as clean as possible. The system should be cleaned properly every time the fluid is changed. All accumulations of solids-chips, fines, extraneous material-should be removed. Solid contamination tends to accumulate in areas where fluid flow is at low velocity. It may be desirable to flush the system with a warm bactericidal solution before new emulsion is charged to the system.
Bacterial growth can be controlled through proper maintenance. A small re-circulating pump operated during downtime will normally provide adequate aeration to help eliminate bacterial growth. This generally means avoiding all contamination with organic materials, which serve as food for the bacteria For example:
- Don’t use the sump as a garbage disposal for food scraps.
- Don’t spit in the sump.
- Don’t throw cigarette butts or matches into the sump.
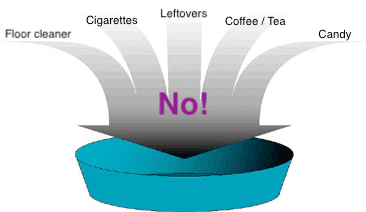
Maintaining concentration is most important
For uniform cutting performance, the oil-water ratio in the emulsion should be kept reasonably constant. However, water is continuously being lost due to evaporation (5-20% daily), particularly where high temperatures are involved. It is good practice to check the water daily, and replace whatever portion has been lost. During use, though, the of salts in the water become concentrated as portions of the water evaporate, resulting in levels of hardness that could cause the emulsion to break. For some large systems, it may be economical to install de-ionizing equipment to remove the dissolved salts. In smaller systems, chelating agents can be used to treat the water.
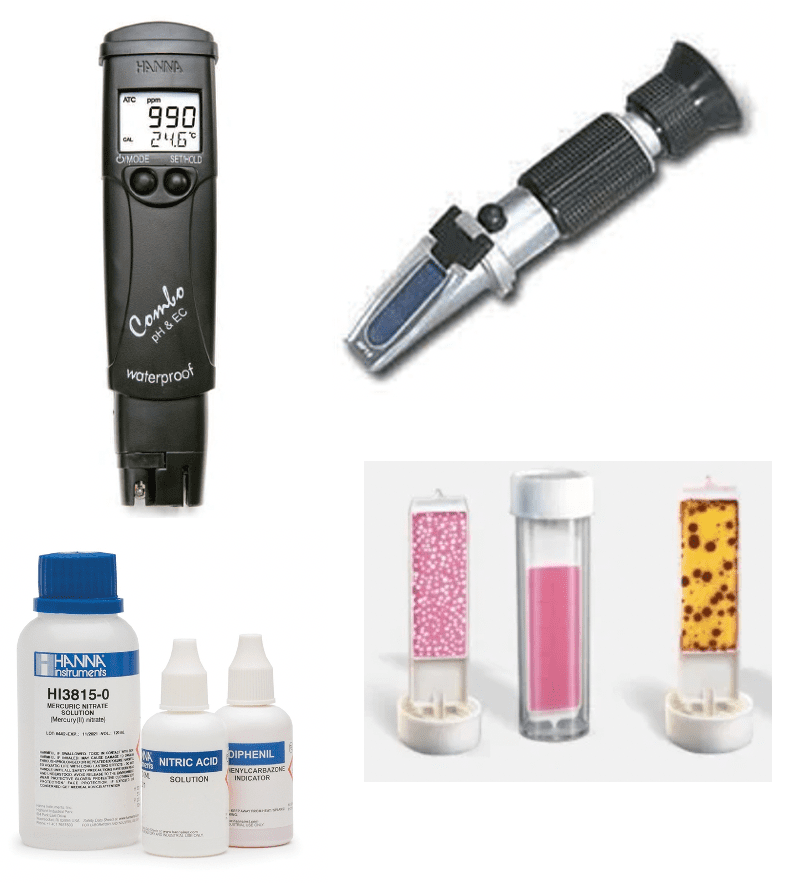